The Capabilities of Precision Tailored to the Requirements of Industry
When purchasing die-cutting machinery, one of the most important factors to take into account is the machine's capacity to fulfill the precise requirements of the industry. It is important to pay attention to the smallest details for manufacturers who rely on die-cutting EMI foam, thermal gap pads, or silicone rubber gaskets. Die cuts with a high degree of accuracy reduce the waste of material and guarantee that components are a perfect fit. This is especially important in industries such as the automotive and electronics industries, where even minute discrepancies can lead to costly faults.
Ability to Adapt to Different Materials
It is essential to take into consideration the adaptability of die-cutting machines in terms of their ability to work with a wide variety of materials. The usage of materials such as die-cutting Mylar Film or Conductive Foam has become increasingly common in recent years due to the proliferation of novel applications such as electric vehicles and smart devices. More value will be provided by machinery that is able to cope with a variety of substrates, such as the dense foil that is necessary for foil heat shields and the precise cutting that is required for die-cut solutions for electric vehicle batteries. The versatility of a die-cutter allows for greater adaptability in manufacturing and offers up new opportunities for the expansion of a firm.
High production rates can be achieved through volumetric efficiency.
During the process of rolling out high-volume orders, which is especially important in situations such as automotive die cutting, the throughput of the machines must not compromise on quality. To ensure that enterprises are able to fulfill the needs of the market without falling short of their delivery obligations or standards, modern die-cutters that are designed to preserve uniformity while rapidly creating huge quantities of components are available.
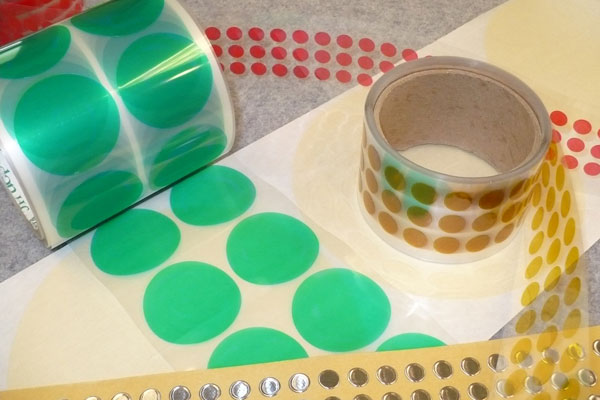
Compatibility with Already Existing Systems
The importance of understanding how a new die-cutter fits in with existing production systems cannot be overstated. Integrating seamlessly guarantees that there is no downtime and helps to maintain the productivity of the workflow. The amount of time spent on training and the amount of production flow that may be improved by machinery that easily interacts and cooperates with preexisting setups is beneficial to companies that are capitalizing on modern fabrication techniques.
Assistance and Dependability Over the Long Term
When your company makes an investment in a die-cutting solution, you are not only committing resources to a machine, but also to a long-term engagement with the manufacturer. It is important to make sure that the machine you choose comes with dependable after-sales assistance and service guarantees. This protects you against unanticipated problems and probable stops in operation. In addition, doing routine maintenance and upgrades helps to ensure that the machine continues to operate at its highest level, which helps to justify the initial investment.
The Cost-Effectiveness Analysis: Initial versus Ongoing Expenses
Although it is possible that the initial cost of die-cutting gear will be large, it is essential to have a comprehensive awareness of the financial environment, which includes the costs of operation and maintenance respectively. Choosing cutting-edge technology such as that offered by suppliers who specialize in broad-spectrum It is possible to lower continuing costs by using Automotive Die Cutting because of its effective use of energy and its quicker setup times. When we talk about budget-friendly machinery, we are not merely referring to lower initial expenditures; rather, we are referring to a more comprehensive view of economic efficiency across the machinery's operational lifespan.
For enterprises, selecting die-cutting machinery that not only meets their current requirements but also corresponds with their long-term production goals and scalability ambitions can be accomplished by giving careful consideration to the aforementioned criteria.
When purchasing die-cutting machinery, it is necessary to carefully consider a number of crucial aspects that have an effect on both the current capabilities and the potential for future capabilities. For the purpose of ensuring that the solution selected increases productivity and maintains excellent outputs on a regular basis, each factor, ranging from the compatibility of materials to the integrability of the system, plays an essential role. It is important to keep in mind that the competitive advantage and operational success of tomorrow's manufacturing excellence are determined by the smart investment in die-cutting technology that is made today and for details. When these issues are investigated, it is possible to acquire machinery that contributes to the achievement of precision, flexibility, and reliability, which are the pillars upon which modern manufacturing flourishes.